How to choose the appropriate spring when installing spring supports and hangers?
Mar 04,2025
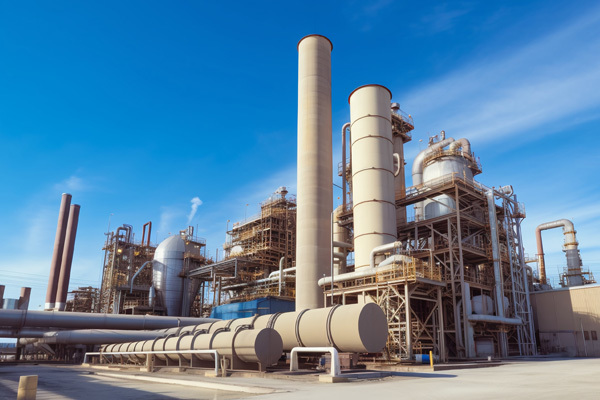
1. Consider the weight (working load) of the pipeline or equipment
-Accurate calculation of workload: Firstly, it is necessary to accurately calculate the weight of the pipeline or equipment, including the weight of the pipeline itself, the weight of the internal medium, the weight of the insulation material (if any), etc. For example, for a pipeline with a diameter of $D $and a length of $L $, its own weight can be calculated by the density of the pipeline material $rho $and the calculation formula $m=rhotemsprotimes (D/2) ^ 2timesL $; The weight of the internal medium is determined based on the density of the medium and the volume of the pipeline. In chemical pipelines, the density of different media varies greatly. For example, the density of water is about $1000 kg/m ^ 3, while the density of some organic solvents may be lower than that of water, all of which need to be accurately considered.
-Matching the bearing range of springs: Springs have their rated bearing range, and the selected spring's rated bearing capacity should be able to meet the working load requirements of pipelines or equipment. Generally speaking, the working load range of a spring should cover the calculated actual working load and have a certain margin. For example, if the actual working load is $1000N $, a spring with a working load range of $800-1200N $can be selected to cope with possible load fluctuations.
2. Consider the displacement of pipelines or equipment (thermal displacement or other displacement)
-Determine the direction and magnitude of displacement: Analyze the possible displacement direction (axial, lateral, or vertical) and displacement magnitude that may occur during the operation of pipelines or equipment. In thermal pipeline systems, thermal displacement is the main displacement factor. The thermal displacement can be calculated based on the material's coefficient of thermal expansion alpha, pipeline length L, and temperature change DeltaT using the formula DeltaL=alphatimesLtimesDeltaT. For example, the thermal expansion coefficient of carbon steel pipes is approximately $1.2times10^ {-5}m /(mcdot^ {circ}C )For a pipeline with a length of $100m, the temperature change is $100^ {circ}C The thermal displacement is $0.12m.
-Choose a spring with appropriate displacement compensation capability: The displacement compensation capability of the spring should match the displacement of the pipeline or equipment. Springs of different specifications have different displacement compensation ranges. It is necessary to ensure that the selected spring can expand and contract normally to adapt to displacement changes in pipelines or equipment, while ensuring that its bearing capacity is within the allowable range. For example, if the displacement of the pipeline is $50mm, a spring with a displacement compensation greater than $50mm needs to be selected.
3. Consider the stiffness characteristics of the spring
-Understanding the influence of stiffness on the performance of supports and hangers: Spring stiffness ($k $) refers to the change in spring force per unit displacement, and its calculation formula is $k=F/Deltax $($F $is the spring force$ Deltax $is displacement). A spring with higher stiffness has a greater variation in spring force under the same displacement change. In some situations where high stability of pipeline support is required, such as pipeline connections for precision equipment, it may be necessary to choose springs with appropriate stiffness to avoid adverse effects on pipelines or equipment caused by excessive changes in spring force.
-Choose stiffness based on actual needs: Select spring stiffness based on the specific requirements of the pipeline system. If the pipeline system needs to maintain a relatively stable support force during displacement, springs with lower stiffness can be selected; If you want the spring force to respond quickly to displacement changes to limit excessive displacement of the pipeline, you may need to choose a spring with higher stiffness. For example, in some pipeline systems with seismic requirements, increasing the spring stiffness appropriately can improve the seismic performance of the pipeline.
4. Consider work environment factors
-Temperature environment: If the pipeline or equipment operates in high or low temperature environments, it is necessary to choose spring materials that can adapt to the corresponding temperature. For example, near high-temperature steam pipelines, ordinary spring materials may lose their elasticity or strength due to high temperatures. In this case, high-temperature resistant spring materials such as high-temperature alloy springs need to be selected.
-Corrosive environment: In environments with corrosive media, such as chemical pipelines transporting acidic or alkaline solutions, springs need to have good corrosion resistance. You can choose springs made of corrosion-resistant materials such as stainless steel, or apply anti-corrosion treatments such as galvanizing or painting to extend the service life of the spring.
5. Consider the fatigue life of the spring
-Evaluate pipeline operating cycle and conditions: For pipeline systems with frequent start stop, temperature or load changes, springs need to have sufficient fatigue life. It is necessary to evaluate whether the fatigue life of the spring meets the requirements based on the operating cycle of the pipeline, the frequency of changes in working conditions, etc. For example, in the pipeline system of the peak shaving unit in a thermal power plant, the operating conditions of the pipeline change frequently, and it is necessary to choose springs with long fatigue life.
-Choose springs with high fatigue life: When selecting springs, refer to the fatigue life data provided by the spring manufacturer. Generally speaking, high-quality spring materials and reasonable spring design can improve fatigue life. For example, springs made of spring steel that has undergone special heat treatment may have a longer fatigue life than springs made of ordinary spring steel. Meanwhile, if the design allows, increasing the size of the spring appropriately can also help improve fatigue life.
Hot Tags:
PREVIOUS:
Contact Us
Email:
ZLWang@huaweibracket.com
Whatsapp:
Sales Phone:
Technical Phone:
Address:
East of Nanzigezhuang Village, Wuning Town, Muping District, Yantai City, Shandong Province
Related Blog