What are the displacement and load inspection methods for spring supports and hangers?
Mar 04,2025
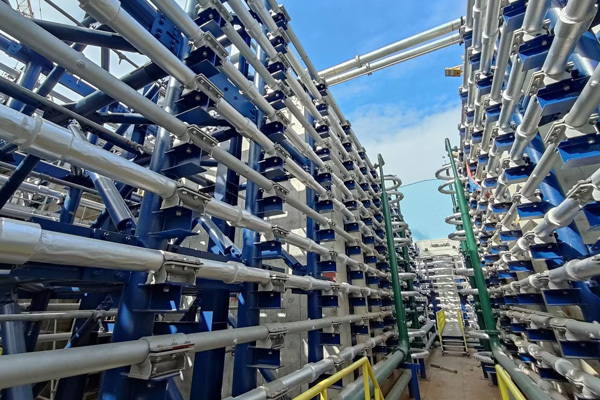
1. Displacement inspection method
-Visual observation and marking comparison
-Principle: Clearly mark the key parts of pipelines and support hangers (such as the connection points between pipelines and support hangers, the ends of springs, etc.). During the operation of the pipeline or during regular inspections, the relative position changes between the markings can be visually observed to preliminarily determine whether the pipeline has undergone displacement at the support and hanger locations, as well as the approximate direction of the displacement.
-Application scenarios and operation steps: This method is suitable for situations where the displacement is relatively large and easy to observe. For example, in some large building plumbing or ventilation ducts, after installation, paint or other marking tools are used to draw marking lines at the corresponding positions of the pipes and support hangers. During daily inspections or regular maintenance, inspectors only need to observe whether the relative positions between these marked lines have changed, in order to quickly determine whether displacement has occurred. If there is a significant deviation in the marking line, further precise measurement methods should be used to determine the displacement.
-Using displacement sensors
-Principle: A displacement sensor is a device that can accurately measure changes in the position of an object. According to different measurement principles, such as linear variable differential transformer (LVDT) principle, capacitive or inductive principle, displacement sensors can convert the displacement of pipelines relative to supports and hangers into electrical signal output.
-Application scenarios and operation steps: Widely used in pipeline systems that require high displacement accuracy, such as high-temperature steam pipelines in thermal power plants or high-precision reaction pipelines in chemical plants. When installing, install the fixed end of the displacement sensor on the stationary part of the support hanger, and connect the movable end to the relevant parts of the pipeline or spring to ensure that the axis of the sensor is consistent with the expected displacement direction. During the operation of the pipeline, displacement sensors measure displacement data in real time and transmit the signal to the monitoring system or data acquisition equipment. Staff can accurately grasp the displacement situation of the pipeline by reading these data.
-Mechanical measuring tool measurement
-Principle: Use mechanical measuring tools such as calipers and dial gauges to measure the relative positional changes between pipelines and supports and hangers. For example, a dial gauge displays the displacement between the end of the measuring rod and the surface of the object being measured by the rotation of the needle, with an accuracy of up to 0.01mm.
-Application scenarios and operation steps: Used in some small pipeline systems or situations where the accuracy of displacement is not extremely high, but more accurate data is required than visual observation. When operating, fix the magnetic base of the dial gauge on the stable part of the support hanger, gently touch the head of the measuring rod with the surface of the pipeline, and read the change value of the dial gauge pointer before and after the pipeline runs or under different working conditions, which is the displacement of the pipeline relative to the support hanger.
2. Load inspection method
-Strain gauge measurement method
-Principle: Strain gauges are sensors based on the strain resistance effect of materials. When the support hanger is subjected to a load, its key components (such as suspension rods, spring seats, etc.) will undergo slight deformation. Attaching strain gauges to these components will cause changes in the resistance value of the strain gauges. By measuring the resistance changes of strain gauges and based on pre calibrated relationships, the strain that the component is subjected to can be calculated, thereby obtaining the magnitude of the load.
-Application scenarios and operation steps: commonly used in situations where high precision load measurement is required, such as pipeline systems in scientific research experimental equipment or high-precision industrial production pipelines. Firstly, it is necessary to select appropriate strain gauges, whose size, range, and accuracy should be determined based on the expected load and deformation of the support and hanger. On the clean and dry surface of the component, firmly stick the strain gauges according to the prescribed bonding process and connect the measuring circuit. During pipeline operation, the resistance change data of strain gauges is read by strain gauges, and the load size is calculated.
-Force sensors directly measure
-Principle: A force sensor can directly convert the magnitude of force into an electrical signal output. For example, piezoelectric sensors utilize the piezoelectric effect of piezoelectric crystals. When subjected to external forces, the piezoelectric crystal generates a charge proportional to the external force. The charge signal is converted into a voltage signal through circuits such as charge amplifiers to measure the output.
-Application scenarios and operation steps: Suitable for pipeline systems of various scales, especially those that require real-time monitoring of load changes. Install force sensors at the connection between the suspension rod or spring of the support hanger and the pipeline to ensure that the sensors can accurately measure the load borne by the support hanger. During the operation of the pipeline, the load sensor transmits the load signal to the data acquisition system or monitoring equipment, making it convenient for personnel to view the load data at any time.
-Calculation verification method
-Principle: Based on the design parameters and operating conditions of the pipeline system, the load of the support and hanger is verified through theoretical calculations. The calculation content includes the weight of the pipeline itself, the weight of the internal medium, the weight of the insulation material, and possible additional dynamic loads (such as fluid impact forces), etc. The vector sum of these forces is compared with the design bearing capacity of the support and hanger.
-Application scenarios and operation steps: Used in the preliminary design verification, regular maintenance inspection, or fault diagnosis of pipeline systems. Firstly, collect detailed design information of the pipeline, such as pipeline size, material, medium parameters, operating temperature, and pressure. According to the relevant mechanical calculation formulas, calculate various load components separately, and then sum them up to obtain the total load. Compare the calculation results with the bearing capacity indicated on the nameplate of the support and hanger or the bearing range specified in the design documents to determine whether the load of the support and hanger is within a reasonable range.
Hot Tags:
Contact Us
Email:
ZLWang@huaweibracket.com
Whatsapp:
Sales Phone:
Technical Phone:
Address:
East of Nanzigezhuang Village, Wuning Town, Muping District, Yantai City, Shandong Province
Related Blog